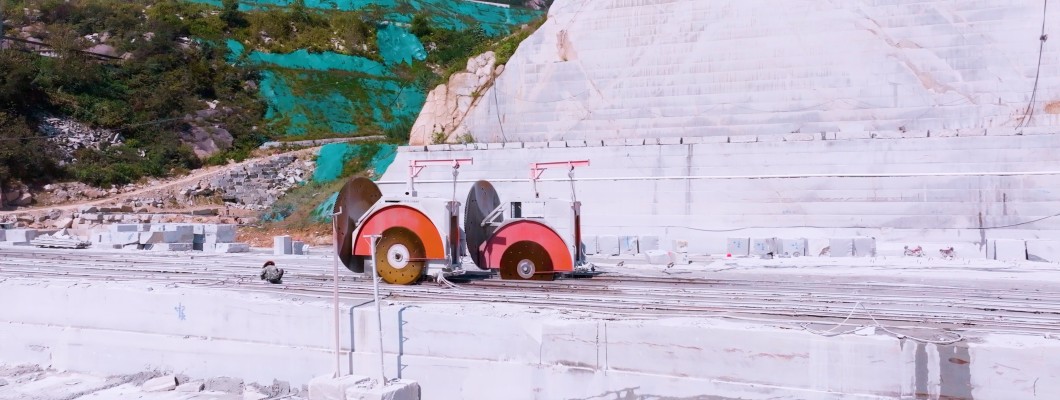
The simple requirements and traits of granite mine exploitation decide that intact stone blocks - difficult blocks assembly sure specifications and with out cracks want to be extracted from the ore body. The layout of the mining working floor and the choice of improvement and transportation tools need to keep in mind the bedding, faults, and fractures of the ore frame, and try to reduce their negative results on mining to make sure the extraction of big - sized tough blocks.
(I) Mining Methods
For granite mine exploitation, first, the first mining area should be decided on in keeping with useful resource situations and marketplace call for, and the mining boundary, mine production scale, and mine operating widespread need to be determined. Mining is carried out based totally on a complete analysis of the natural environment and economic - technical conditions. The mining procedure can be divided into development and transportation, stripping, and mining.
The mined mountain desires to strip the surface soil, weathered layers, interlayers, gentle rocks, and fragmented and non - precious components of the ore.
The basic strategies of granite mining are: separation, splitting, and shaping.
- 1.Separation Process: Common strategies include fracture separation, drilling and blasting separation, flame slicing separation, and blended separation.
- Fracture Separation: Multiple iron wedges may be without delay driven into the rock at certain durations to make the rock crack as required. This technique is suitable for small - scale mines, with low value however also low performance. Another technique is to use hollow - drilled expansive agent for separation. The expansive agent is nicely - blended with water and poured into the drilled row holes. The expansive pressure generated by the placing of the expansive agent is used to crack the rock. This approach is easy and secure but has low efficiency.
- Flame Cutting Separation: A speedy flame is ejected from the flame - reducing nozzle to heat and impact the rock. Due to the distinct thermal response characteristics of various minerals in the rock, it reasons cracking and peeling, progressively forming a separation trench. This approach is handiest applicable to rocks with excessive quartz content, low thermal conductivity, and negative heat switch, which include granite, diorite, syenite, and many others.
- Drilling and Blasting Separation: The rock drill drills row holes inside the rock, and in step with requirements, blasting substances (presently used consist of black powder, combustion sellers, detonating cords) are loaded for controlled blasting. This approach is tremendously efficient and widely used, but the blasting pressure have to be strictly managed all through use to save you harmful cracks.
- Splitting Process: The stone strips separated from the rock are overturned with the aid of a stone - jacking system (or stone - jacking bag), after which, relying on the crack pattern and the specifications of the tough block, the stone strips are cut up into the desired rough blocks by the fracture method.
- Shaping Process: For the cut up rough blocks that don't meet the requirements, shaping is essential. The not unusual strategies are to use a hand - hammer to strike the drill rod or a shaping device to cast off the unnecessary parts of the difficult block to make it flat and feature neat edges.
- Combined Principle Mining of Circular Saw and Bead Saw
- At present, in some marble mines in China, the mining method of mixing circular - saw - kind rough - block stone slicing with guide hollow - drilling and wedge - driving fracture separation of the stone floor has been efficiently carried out. In order to facilitate contrast with the preceding several mining methods, the diamond bead - saw cutting of the horizontal backside of the stone is used to update the guide hollow - drilling and wedge - driving fracture separation of the stone floor, forming any other all - saw - reducing mining method.
- The mixed - principle mining process method of the round saw and bead noticed become first utilized in Fujian, China. This mining approach directly makes use of a circular - saw - kind tough - block stone - reducing system to cut the vertical aircraft in the ore frame, and the horizontal plane adopts a semi - mechanical mining technique of guide wedge - using fracture separation. The bead noticed is used to cut the horizontal backside of the stone, changing the manual wedge - riding fracture separation. This approach is appropriate for medium - and small - scale mechanized marble - mining mines with intact ore bodies.
- The predominant procedure of the blended mining method of the circular saw and bead saw is to apply the diamond bead noticed to separate and cut the horizontal bottom of the separated body. The circular - noticed - kind rough - block stone - slicing machine cuts the separated body into hard blocks according to the specs of the difficult blocks on the separated - frame stone while averting cracks. The next equipment displacement and lifting, and the displacement, lifting, and transportation of the hard blocks are similar to those of the previously introduced numerous mining methods.
- Fire - Baking and Hole - Drilling Mining Method
- The fire - baking and hole - drilling mining technique mentioned here is a method of the use of flame reducing, cooperating with a hand - held rock drill for guide drilling of slicing holes, and combining with detonating cords for controlled blasting to mine marble. The system approach and production procedure of the fireplace - baking and hollow - drilling mining technique. The hearth - baking and hollow - drilling mining method is currently the fundamental approach for marble mine exploitation in China and also the most used marble - mining technique. The predominant mining production process of the fireplace - baking and hollow - drilling mining method is much like that of the manual mining method. In order to make the separation of the separated body from the ore body easier and extra dependable, a fire - baking cutting method of the use of flame reducing to reduce and separate one connection floor of the separated body from the ore body is brought, in order that the separated frame is only linked to the ore body via one vertical aircraft and one horizontal bottom. In the following blasting separation of the separated frame, a - side controlled - blasting situation is fashioned, making the separation work easier and extra reliable. Except for the fire - baking separation of one floor of the separated body, the alternative processes are similar to the previously delivered manual mining technique.
- Manual Hole - Drilling and Bead - Saw Mining Method
- The guide hollow - drilling and bead - saw mining method discussed here is a mining technique that makes use of a diamond bead saw cooperating with a hand - held rock drill to drill slicing holes and combines with detonating cords for controlled blasting.
- The mining manufacturing technique of the guide hollow - drilling and bead - saw mining approach. The manual hollow - drilling and bead - saw mining method is a complicated mining method to update the fireplace - baking and hollow - drilling mining approach for marble mining.
- Except for the separation and reducing manner of the separated frame, the subsequent tactics inside the mining manufacturing manner are the same as those of the fire - baking and hole - drilling mining technique. In this mining approach, the bead noticed replaces the flame reducing to cut one floor connecting the separated body and the ore body. In order to facilitate contrast with the fire - baking and hollow - drilling mining method, we best introduce the approach of using a diamond bead noticed to cut the vertical internal hole of the separated frame, and guide operation of a portable rock drill to drill slicing holes at the vertical contrary aspect and the horizontal backside of the separated body, and mixing with detonating cords for 2 - facet managed blasting to separate the separated body from the ore body.
- In addition, the approach of the use of a bead noticed to cut the horizontal bottom and the use of - aspect blasting to split the opposite vertical planes can also be followed; the approach of the usage of a bead noticed to reduce the vertical inner hollow and the horizontal bottom and using single - layer blasting to separate the final vertical contrary side can also be followed; if the situations permit, the bead noticed can even be used to reduce and separate all 3 connection surfaces of the separated body and the ore body, after which the method of using guide reducing - hole drilling blended with controlled blasting to break up the separated body may be used for mining.
- All - Saw - Cutting Mining with Diamond Bead Saw
- The all - noticed - cutting mining method with a diamond bead noticed mentioned here method that the separation of the separated frame from the ore body, the fragmentation of the separated frame, and the shaping of the difficult block are all finished with the aid of the bead - saw reducing, just like the way of mining marble mines.
- The procedure method and method necessities of all - saw - cutting mining with a diamond bead saw.
- As long as the mining cost is appropriate, all - saw - slicing with a diamond bead saw is currently the first-rate technique for mechanized marble mining.
- Use a diamond bead saw to split and cut all three connection surfaces of the separated body and the ore frame; use a unique pneumatic jacking bag that may be inserted into the cutting seam of the bead - saw rope to jack the separated body far from the ore frame, after which, with the assistance of an excavator, a loader, or a gradual - transferring crane, overturn the separated body; nonetheless use the bead saw to fragment - saw the separated body and shape - reduce the six surfaces of the rough block. To reduce the mining cost, below appropriate situations, manual operation of a transportable rock drill for reducing - hole drilling, expansive agent (expansive cement), or a huge - diameter circular - noticed device can also be used to shape the tough block; with the assist of an excavator, a loader, a derrick crane, or a slow - moving crane, the completed hard block is displaced to the difficult - block stockyard at the mining face and loaded and transported away. The motion of the bead noticed to exclusive slicing positions within the mining discipline is also finished by an excavator or a loader.
- Platform - Mounted Rock - Drill and Bead - Saw Mining Method
- The platform - established rock - drill and bead - saw mining technique is an advanced mining method that replaces guide operation of a transportable rock drill and flame slicing for marble mining. This mixed mining approach originated in the early 1990s. With the improvement of the technical overall performance of diamond bead - noticed ropes used for mining and cutting marble and the reduction of production costs, it has now turn out to be the maximum widely used and across the world identified quality technique for mechanized marble mining. In most important marble - tough - block - generating countries which includes Italy, Brazil, Mexico, and India, this mining technique may be very famous and has grow to be the simple technique for mechanized marble mining.
- Introduction to the method method of the platform - established rock - drill and bead - noticed mining technique.
- The mining technique of the platform - installed rock - drill and bead - saw mining approach is similar to that of the manual hollow - drilling and bead - saw mining technique, besides that a platform - set up rock drill is used to replace the hand - held rock drill operated manually for drilling slicing holes, and the entirety else is the equal.
- According to the wide variety of connection surfaces of the separated frame and the ore body cut through the diamond bead noticed, the mining is split into three schemes for value calculation. That is, Scheme 1: The bead noticed handiest cuts the vertical internal hole of the separated body. Scheme 2: The bead saw cuts the horizontal backside and the vertical internal hollow of the separated body. Scheme three: The bead saw cuts and separates all three connection surfaces of the separated body and the ore body. For the connection surfaces of the separated frame and the ore frame that aren't reduce via the bead saw, in addition to the following fragmentation of the separated body and the shaping of the rough block, the platform - set up rock drill is used to drill slicing holes and mixed with detonating cords for managed - blasting operations.
(II) Technical Requirements
Under regular conditions, when the production stripping ratio is ready 0.3, the minimum monetary block rate of the granite mine is 15% - 25%.
- Quarry Bench Dimensions
- When the use of a mobile crane, the bench dimensions are 4 - 6m.
- When the usage of a small - sized gantry crane, the bench dimensions are less than or identical to 14m.
- When using a huge - sized gantry crane, the bench dimensions are less than or equal to 62m.
- The slope angle of the sub - bench is commonly 90°, and the final slope perspective is decided according to the rock balance situations.
- Stone - Strip Width
- The width of the stone strip is decided consistent with the characteristics of the mining system, the specifications of the tough block, and the crack situations, usually 1 - 3m.
- Working - Surface Length
- For guide mining, it's miles commonly 5 - 15m.
- For flame - slicing mining, it's miles usually 15 - 20m.
- Minimum Working - Platform Width: Generally 20 - 25m.
Leave a Comment