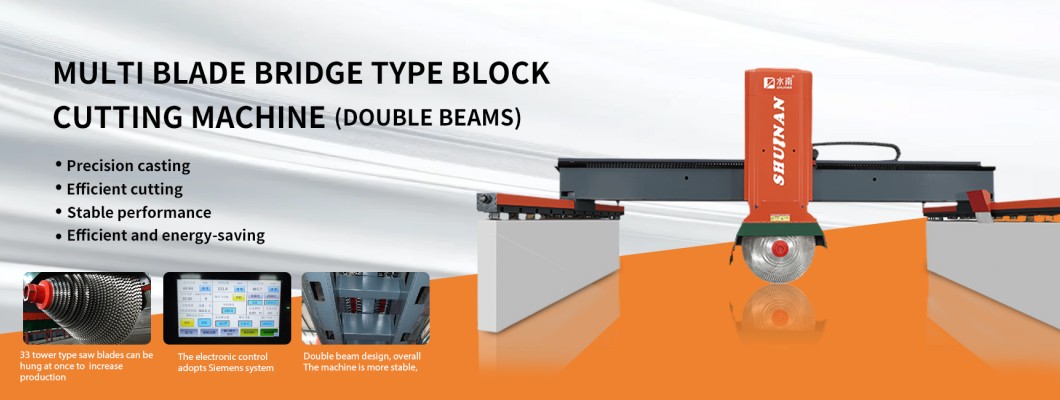
1.Double girder structural design and rigidity enhancement
Shuinan Machinery adopts a double-beam bridge structure (similar to a gantry-type frame), forming a high-rigidity support system through symmetrically distributed box-shaped girders. This structure uses the square tube butt welding process, combined with the overall high-temperature quenching treatment, which increases the bending moment of inertia of the equipment's cross-section by more than 30%. It effectively suppresses the vibration and deformation caused by the stress release of the stone during the cutting process. Experimental data shows that when cutting granite with a Mohs hardness of ≥7, the structural deformation can be controlled within 0.05mm/m².
2.The Synergistic Effect of the Precision Guide Rail System
Selection of Imported Linear Guide Rails
The linear guide rails of grade 7 precision from THK in Japan or HIWIN in Taiwan are adopted, equipped with sliders whose preload can be adjusted. While eliminating the axial clearance, it maintains a linearity of travel of 0.003mm/300mm. Compared with the traditional sliders, its roller design increases the load-bearing capacity by 2.8 times, and it is especially suitable for the impact loads during stone cutting.
Technology of Closely Ground Guide Rails
As an alternative special guide rail, after being processed by a precision grinder, the surface roughness can reach Ra0.2. Together with the automatic dust removal scraper, it ensures that the repeated positioning accuracy remains at 0.005mm even in an environment full of stone powder. The parallelism of the guide rails is calibrated by a laser interferometer, and the error is ≤0.01mm/m.
3.The Dynamic Precision Control System
Servo Drive Technology
The Σ-7 series servo motors of Yaskawa are adopted, and in combination with a 32-bit DSP controller, an interpolation accuracy of 0.1μm level can be achieved. The dynamic response time is ≤3ms, which effectively suppresses the trajectory deviation caused by the cutting recoil.
Error Compensation Mechanism
It integrates a dual closed-loop compensation for temperature and vibration. Through 12 sensors distributed on the crossbeam, it can correct thermal deformation and mechanical resonance in real time. Together with the plate straightening algorithm 1, it can automatically compensate for the deformation of 0.3-0.8mm caused by the natural texture of the stone.
4.Verification of the Actual Cutting Performance
In the continuous 8-hour cutting test (stone specifications: 3000×2000×600mm):
Surface flatness: ≤0.8mm/m² (The national standard GB/T 18601 requires ≤1.5mm)
Diagonal error: ≤0.6mm (Better than the 1.2mm specified in JC/T 507-2012)
Repeat processing accuracy: ±0.03mm (200-cycle test)
Through the rigid guarantee of the double-beam structure, the stable guiding of the precision guide rails, and the synergistic effect of the intelligent compensation system, this equipment has successfully reduced the surface error of traditional stone cutting from 3-5mm to within 1mm. It is especially suitable for the industrial production of high-end stone products such as high-precision curtain wall panels and countertop panels.
Leave a Comment