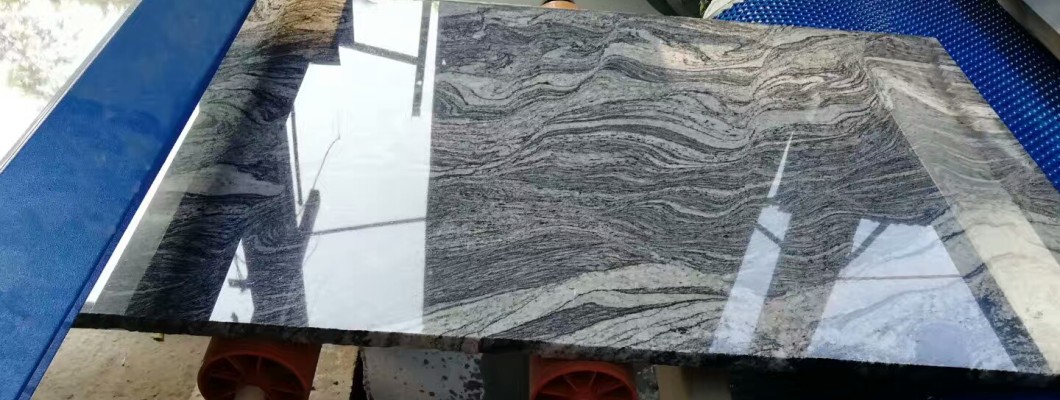
Introduction: Granite, with its durability, unique aesthetic, and variety of colors, is widely used in construction and decoration. From raw material to the final slab, every step of the processing is crucial to the quality and appearance of the finished product. This article will provide a detailed look at the granite slab processing process, helping you better understand this complex craft.
1. Selection and Mining
The processing of granite begins with mining. First, the right quarry and quality raw material must be chosen. The size and quality of the raw material greatly affect the subsequent processing.
During the mining process, large cutting equipment is used to extract granite from the rock layers, and these raw blocks of granite are referred to as "rough blocks."
2. Transportation to the Processing Plant
After mining, the granite rough blocks need to be transported to the processing plant by truck, ship, or rail. Special care is required during transport to prevent surface damage to the rough blocks, as this could affect the subsequent processing.
3. Cutting into Slabs
Once the rough blocks arrive at the processing plant, the first step is to cut the granite into slabs of varying thicknesses. This is typically done using large stone cutting machines.
Common equipment includes bridge saws, which use high-powered blades to cut the stone. During this process, operators must carefully control the cutting depth and angle to ensure uniform dimensions of the slabs.
4. Flattening and Polishing
The surface of the cut slabs is often uneven and rough, so flattening and polishing are necessary. This step uses large grinding discs to smooth and level the surface, removing any obvious cutting marks or imperfections. The quality of the flattening process will directly impact the final appearance of the slabs.
5. Cutting and Edging
Sometimes, slabs need to undergo further cutting and edging to meet the specific requirements of the customer. Precision cutting equipment is used for customized processing, including fine edge trimming and hole drilling. This ensures that the slabs meet the required dimensions and shapes for the project.
6. Polishing
Polishing is a vital step in granite processing, as it enhances the shine and aesthetic appeal of the granite slabs. This process usually involves using grinding stones with varying grit sizes to progressively smooth the surface, ultimately achieving a mirror-like finish. High-quality polishing not only adds to the slab's visual appeal but also increases its durability.
7. Quality Inspection
Each granite slab must undergo strict quality inspection during the processing. Inspection criteria include the thickness, dimensions, surface finish, and checking for any cracks or imperfections. High-precision inspection equipment ensures that every slab meets the required standards.
8. Packaging and Shipping
Finally, the qualified granite slabs are packaged, typically using wooden frames, steel bands, and foam to provide protection and ensure that no damage occurs during transportation. Once packed, the slabs are shipped to customers or construction sites, ready for use.
Conclusion:
From rough blocks to the final qualified granite slabs, each processing step plays a critical role. The precise operation at each stage ensures that granite slabs not only possess an attractive appearance but also meet the durability requirements for practical use. By understanding this processing flow, we can better appreciate the unique charm of granite and help industry professionals optimize their processing techniques to improve production efficiency and product quality.
Leave a Comment