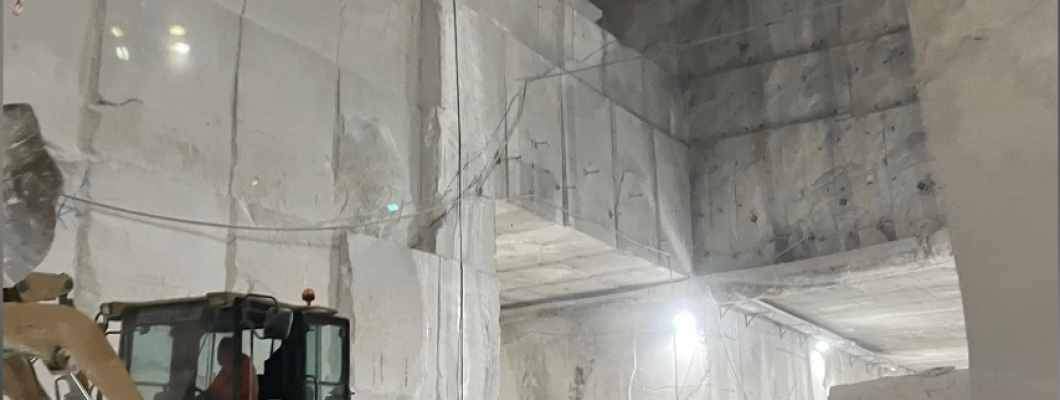
Marble Underground Mining Technology and Comparative Analysis with Open-Pit Mining
I. Underground Mining Process Flow
1. 3D Exploration & Positioning
Utilizes geological radar (100MHz frequency) combined with core sampling (Φ110mm drill bit) to precisely locate high-quality ore veins, establishing a 3D underground model with positioning accuracy of ±0.5m.
2. Tunnel Excavation
Employs TBM (Tunnel Boring Machine, 3.5m diameter) to advance along ore veins, with simultaneous installation of steel arch supports (0.8m spacing). Ventilation systems maintain oxygen concentration >19.5%.
3. Mechanical Cutting
Diamond wire saws (11mm diameter) cut along vertical joint surfaces at 0.8-1.2m²/h, assisted by high-pressure water mist dust suppression (3.5MPa pressure).
4. Block Transportation
Custom rail carts (15t capacity) transport blocks through inclined tunnels (8° slope), with in-tunnel haulage distance limited to 500m.
II. Comparative Analysis with Open-Pit Mining
Indicator | Underground Mining | Open-Pit Mining |
Mining Depth | Underground 50-200m | Surface to -30m |
Resource Recovery | >85% | 60-70% |
Cost per m³ | ¥380-450/m³ | ¥220-280/m³ |
Environmental Impact | Surface disturbance <0.5ha | Damage area >20ha |
Operational Cycle | Year-round operation | 30-60 rainy-day shutdowns |
Safety Incident Rate | 0.12% | 0.08% |
Key Difference: Underground mining achieves "point development," while open-pit causes "areal destruction." Tunnel support accounts for 35% of total underground costs, versus 18% for open-pit reclamation expenses.
III. Technical-Economic Analysis of Underground Mining
1. Geological Adaptability
Optimal for steeply dipping deposits (>60° inclination), e.g., Cangshan Mine in Yunnan. Efficiency drops 40% for horizontal ore bodies.
2. Economic Threshold
Economically viable when deposits meet:
Block recovery rate >50%
Ore body thickness >8m
Proximity to sensitive areas (<1km from settlements)
3. Innovation Trends
5G remote control systems reducing underground risks
Real-time laser scanning modeling (±2cm accuracy)
Backfill mining (waste recycling rate >90%)
Case Study: Italy's Carrara mining area maintains 120km+ tunnels with 100-year continuous production, achieving 25% higher recovery than open-pit. Currently, China's underground mining accounts for <8% of total production, projected to reach 20% by 2030 under ecological red line and smart mining policies.
This technology proves particularly suitable for urban periphery mines and scenic protection zones. Although initial investments are 60% higher, full lifecycle benefits increase 2-3 fold.
Leave a Comment