27 Feb
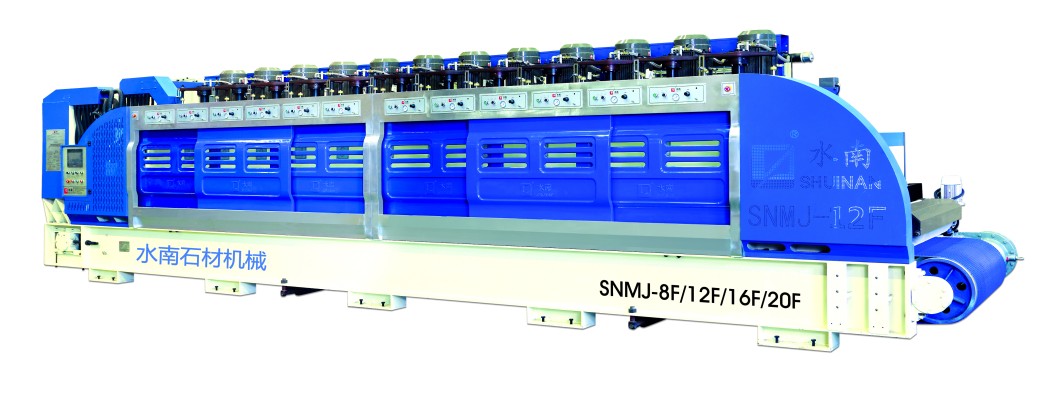
Posted By
0 Comment(s)
126 View(s)
Granite stone plate processing era
Granite plate processing generation
Granite is a high hardness stone, its Mohs (Mohs) hardness is set 6, processing trouble. Later, because of the huge application of artificial diamond gear, which makes the speedy development of the granite processing industry, has emerge as the most broadly used and the largest use of natural finishes.
Granite utility range is very wide, whether or not indoor or outdoor, cottage or square constructing, everywhere you may see its shadow, which is the most widely used at the granite plate, the largest range of transactions is the granite plate magnificence of products.
I. Granite plate processing techniques
Although the application of granite slabs, a extensive variety of merchandise, a huge range of merchandise, paving stones, specification plate, small rectangular, curved plate, corners, lines and so forth. But the main processing of granite isn't always complicated, its simple processing strategies are: sawing, grinding and polishing, reducing processing, chiseling, burning processing, auxiliary processing and inspection and restore.
1) sawing
Sawing is a stone sawing system might be reduce into granite barren plate (general thickness of 20mm or 10mm), or strips, blocks and other shapes of semi-completed products. The process is a roughing technique, the technique has a widespread impact on the price of barren plate, plate nice, the monetary advantages of firms.
The main processing equipment inside the sawing process is a unique body type large automated sanding saw for granite, multi-blade -manner slicing gadget, multi-blade pc-managed granite reducing gadget and granite disc sawing gadget and so forth.
2) Grinding and sharpening
The cause of grinding and sharpening is to further system the sawn slabs so that their thickness, flatness and gloss meet the necessities. The manner first needs to be difficult grinding and leveling, after which regularly through the semi-first-class grinding, excellent grinding, best grinding and sprucing, the granite coloration texture completely display.
The most important processing device are: automatic multi-head non-stop grinding system, diamond leveling device, bridge mill, disk mill, reversing rough grinding machine, handheld grinding system.
three) Cutting Processing
Cutting method is to apply the cutting device may be difficult or polished plate in line with the desired specs for the scale of the shaped reducing system.
The essential processing equipment is a longitudinal multi-noticed blade cutter, horizontal cutter, bridge cutter, cantilever cutter, hand crank cutter.
4) Chiseling
Chiseling is a traditional processing technique, via the wedge, chiseling, cutting, trimming, grinding and other methods of processing the embryo into the desired products, the floor can be pineapple floor, longan surface, lychee floor, herbal floor, mushroom surface, ragou surface and so forth.
Chiseling and slicing is mainly used for guide processing, consisting of hammer, chopping awl, burin, chisel, and so on., however some of the processing can be finished the use of machine processing, the primary gadget is a stone splitter, stone planer, computerized hammer and chisel device, automated sandblasting device.
five) Burning
Burning processing, additionally referred to as burning processing, spray burning processing, is the use of granite composed of different mineral particles of the thermal growth coefficient of distinction, with the flame burning to make the surface of a number of the debris of thermal expansion rupture and fall off, the formation of undulating and orderly tough surface ornamentation. This form of rough granite plate
This form of difficult granite plate is very appropriate for the ground ornament in slippery places and outside wall ornament.
The main system is granite computerized burnishing gadget.
6) Auxiliary processing
Auxiliary processing is the stone has been reduce and polished according to the desires of grinding, chamfering, commencing holes, drilling, milling grooves, milling and so forth.
The primary processing device are automatic grinding and chamfering system, profiling milling machine, thin-walled drilling gadget, handheld diamond circular noticed, handheld grinding and polishing system.
7) Inspection and repair
Natural granite unavoidably have cracks, holes and different defects, and in the processing process will inevitably have some bumps, some small defects. So all granite slabs want to be inspected after processing is finished, first of all thru cleaning, then blow-drying inspection, certified merchandise are packed into the warehouse, while unqualified products have to be picked out first. In line with the necessities of the order, for a few defects are not extreme granite merchandise can be repaired, i.E., bonding, restore, thereby lowering the scrap price.
Inspection and repair is commonly guide paintings, however some advanced processing manufacturing line will use computerized non-stop blowing and repairing air drying machine.
Translated with DeepL.Com (unfastened version)
II. Granite plate processing technology waft
There are four essential production lines for the processing of granite slab kind merchandise:
Specification plate manufacturing line, thin plate manufacturing line, hard floor decorative plate manufacturing line and shaped plate manufacturing line.
1. Granite specification plate processing era go with the flow
The use of cranes could be loaded on the barren fabric car, the ferry car sent to the frame sanding saw role sawing into the gross plate, after which despatched to the grinding, sharpening, cutting and different methods into the mild plate, and in the end via the inspection and packaging into the warehouse.
The fundamental method:
Raw cloth lifting → sawing → rinsing inspection → tough grinding → quality grinding → quality grinding → sprucing → reducing restore → inspection and packaging
2. Granite plate processing generation float
Granite sheet processing is largely accomplished with automatic processing line, the technique is basically similar to the processing of specification plate, the system is hooked up by means of the curler, unloading gadget, flap gadget.
The essential method:
Wasteland lifting → sawing into skinny plate → reduce off → grinding and polishing → reduce off → grinding, chamfering, milling slot restore, cleaning, drying → inspection and packaging
3. Granite difficult floor decorative plate processing era glide
Granite semi-finished plate via the raceway to ship automatic chiseling system (consistent with the specified sample thickness of the chosen cutter head), the cutter head in line with the predetermined music chiseled out quite a few coarse decorative patterns required. If you need to burnish the board, the board will be despatched to the automated burnishing gadget processing.
The primary manner:
Semi-finished boards → chiseling or burnishing → slicing → inspection and packaging
4. Shaped plate processing generation drift
According to the special requirements of users of granite plate shape, specifications, layout and manufacture of templates, such as round, oval computer, elliptical holes lavatory counter tops, window prisms, and so forth., and then copy the form of the milling device in line with the form of the template (or the microcomputer preset program) inside the semifinished plate processed out of the required form.
The predominant procedure:
Semi-completed plate → slicing side → formed milling → drilling → grinding and chamfering → inspection and packaging
Classification of herbal stone carvings and its processing generation float
Natural stone carving is a very rich artistic fee, very ornamental stone crafts. According to the carving method and floor modeling, it's far mainly divided into 4 kinds: round carving, remedy, line carving and shadow carving.
Round carving
Also known as 3-dimensional carving, refers to non-compressed, may be multi-directional, multi-attitude appreciation of 3-dimensional sculpture, is the overall overall performance of artwork inside the carving, it desires to be carved from six aspects of the entire variety of carving, so that the viewer can see the various facets of the object from special angles.
Relief sculpture
Relief sculpture is a combination of sculpture and portray merchandise, is carved on the aircraft of the concave and convex undulating image of a sculpture, is between the spherical carving and portray between the inventive expression.
Line Carving
Line carving is a sculpture that uses negative or effective strains as a means of modeling, but the stone is in particular carved with bad strains, so it is also known as sunken carving. This kind of carving method absorbed Chinese portray and meaning, overlapping, line modeling scatter perspective and other conventional penmanship, stone by way of plane processing grinding and sharpening, tracing sample text, and then in line with the figure engraved on the road, to the extent of the road thickness and depth, the use of shadows to reflect the 3-dimensional sense. Most of these merchandise are used for the exterior surface ornament of homes, with a sturdy inventive.
Shadow Carving
Shadow carving is a new stone carving technique created with the aid of stone carvers in Hui'an. It is a strong color stone (generally black), first by using the surface grinding, and then in line with the black and white mild and darkish imaging principle, via the pointy and exceptional tools carved out the size, depth, sparse and dense microdots, like the early black and white pics depend upon one of a kind black and white levels to specific the sample. However, with the improvement of era, now additionally appeared in coloration shadow carving.
Of course, stone carving artists will also integrate the above four carving method to create a few complete and complex stone art carvings.
Although there are numerous sorts of stone carvings, distinct shapes, however their processing technique is normally the same. Usually a stone carving is finished through those procedures:
1. Selection of stone 2. Conceptualization of the model three. Carving hard 4. Crowning glory of the shape 5. Info of the carving 6. Floor remedy 7. Cleansing protection
The following specifically to the spherical carving as an example, do a specific advent.
Selection of substances and mould will not be added, in particular to introduce the process of carving methods.
Round carving method in accordance with the enterprise's jargon is more or less divided into the opening, playing high-quality and polishing 3 steps.
I. Opening
The process of starting is almost identical to the two parts of carving the hard and finishing the modeling introduced in advance, however according to the round carving, this may be divided into three stages:
Open huge wasteland - the stone blanks chiseled away the extra, until the carving of the preliminary define of the overall outline of the chisel.
Open within the wasteland - is the carving of the general define of the similarly hammering out the frame and floor courting between the basic shape to.
Open the small barren - is to similarly the carving process chiseling to the completed size from about 1 centimeter thick or so.
Of course, because of the different conduct of every stone carver, so the processing of the three procedures will every now and then trade, there's no constant software. The process is specifically using large, medium and small burin and other tools, but now essentially changed with electric or pneumatic gear.
Second, playing first-rate
Playing exceptional is the the front “open small desolate tract” left by the excess a part of the chisel off, carving the picture and shape of the information. Play great is an crucial degree of creative remedy of stone statues, a carving proper and horrific all in this stage, need staying power carving. The predominant gear used within the first-class-toothed chisel, flat chisel, stone setback, and so forth..
Third, sharpening
Polishing is in the first-rate stone carving on the idea of the very last photo of the preferred inventive impact, with grinding equipment at the carving of the complete body or nearby grinding, sharpening, so that it will spotlight the feel of the stone, add stone carvings of the smooth effect, to enhance its inventive infectious pressure. Polishing gear needed when sprucing system, grinding wheel, sandpaper, polishing paste, and many others.. Of course, in line with the distinctive requirements of the designer of direction, acid etching, sandblasting way of surface processing. If it's miles divided into components of the carving to be assembled first, on the meeting is not suitable for the area to modify and then polished.
Finally is to carry out cleaning and renovation. Is to wash clean the stone at the dirt stains and sticky and residual glue and so on. According to the kind of stone and layout necessities, on the required shielding agent or varnish. Finally smooth sassafras wipe easy.
Stone countertop production system
Stone counter tops particularly consist of: granite countertops, marble counter tops, sandstone counter tops, slate countertops, limestone countertops and quartzite counter tops, of which the mainstream is granite and marble counter tops, and the quantity of manufacturing and application, granite countertops are the maximum large.
The main processing waft of stone countertop is:
Selection of materials → large reduce → grinding → slicing → side processing → digging pots drilling → grinding restore → take a look at splicing inspection → packing → of completion
Material choice
According to purchaser samples or production order necessities to select the appropriate raw barren stone, it is first-rate to knock a small sample of barren cloth for polishing manage, commentary of pattern, colour and particle consistency. If it is a everyday thickness of the countertop can also go to the slab marketplace to without delay buy slabs. Selection of cloth is to pick the identical colour, the equal sample, the identical debris, near the density of the barren fabric or plate, at the same time as the advent does no longer allow cracks, stone gall, colour line, flower sweep and other defects. At the same time, we should pay attention to the thickness and size.
Large reduce
It is the process of reducing the barren fabric into difficult boards with circular saw or sand noticed in keeping with the processing requirements of customers. After reducing, we ought to perform an inspection first, certified forums to live, unqualified select out, for the exceptional-thick boards for the fixed put up-processing. (If the acquisition is a huge board, you may bypass this level.)
Polishing
Polishing level is divided into elements: tough grinding and great grinding.
Rough grinding: the certified products of the preceding method and the fixed thickness of the woolen plate with a grinder for tough grinding, the modern grinding gadget is mainly hand held mill and multi-head continuous grinding and sharpening device. After the board is dry, test the board, the board effect is ideal, you could immediately great grinding, in case you find the board board first-rate isn't always perfect, you may brush the floor of the board to deal with the glue, brush a layer of resin glue could be above the board of small holes and cracks, chook claw pattern and other defects to make up for the best, however additionally make the board of the board of the board is better, extra smooth. In proper weather conditions, the resin is usually more than half of an hour to dry, if the climate is not good, almost 1-2 hours to dry, it is first-rate to wait for the dry and then nice grinding. There are also factories that wash and check the wool forums without rough grinding, and after that brush the glue immediately at the wool forums (those with troubles). Usually granite is brushed less and marble greater.
Fine grinding: with the grinder can be certified or repair the gross plate after the gross plate one after the other grinding processing into the gross light plate, recall to the gross mild plate can't be repaired in the cracks, coloration mild, stone gall bladder, sweeping flora and different defects with a pink crayon within the plate mark out, in order that the subsequent process to timely detection, can keep away from those defects used to system small-size additives which includes water blocking off boards or thickened facet and so on. Usually European and American orders to acquire the gloss requirements in more than 90 ° (or according to consumer requirements processing, if part of the stone species can not meet the necessities to be negotiated with the purchaser). At the identical time, the flatness restrict tolerance of European and American trendy tough board is 0.8MM, and the thickness restriction tolerance is plus or minus 1MM.
Edge reducing
The front qualified difficult board in keeping with the requirements of the manufacturing order for cutting, slicing the advent of the numerous components of the panel - the principle countertop, while the returned of the baffle, aspect baffle and the front baffle and so on. Cutting need to pay attention to the floor before checking, be aware of the previous marked stone defects, to keep away from cracks, black spots, color traces, shade spots, swept flowers, and so forth., do now not have yin and yang surfaces. At the same time to ensure that the geometry of the finished product after reducing, angle size, diagonal size is accurate, do no longer allow chipped edges, drop nook phenomenon. If the again of the countertop panel needs to be bonded, it's also necessary to make sure that the lower back of the rims, edges and corners are intact, in an effort to facilitate the edge processing afterwards.
Edge processing
Edge processing is the brink of the countertop processing processing to peer whether or not it's miles a easy grinding immediately facet or processing right into a fashioned edge (bullnose edge, duckbill aspect, and so forth.). If the customer does no longer require the threshold to be thickened, the countertop may be directly processed aspect processing (edging), if the patron is needed to be thickened part, then the brink of the countertop to be thickened first. Specific practice is to add the primary region after a small cutter grinding, after the bonding surface roughing right into a brown floor, with the intention to more firmly bonded, accompanied by using the utility of adhesive bonding, and ultimately clamped with a clip shape clamped firmly. Pay interest to the bonding time to take note of the bonding floor of the gap among the 2 forums to be as small as feasible, preferably up to 0.1 ~ 0.2 mm. And so forth the glue is dry after the threshold processing can be finished, advanced factories are using a unique imitation part grinding system plus artificial sprucing assistance, wellknown factories are using manual cutting and grinding.
Drill holes for digging basin
It is in the countertop panel to open the sink mouth, faucet holes and undercounter basin set up holes. The holes are usually cut by using machines, and the basin mouth is typically opened manually, or the four corners of the wash basin are first opened via the empty gadget and then cut by way of hand.
Polishing and repairing
Repair is to restore the processing accidentally resulting from the damage (moderate unevenness or lack of corners, and so forth.) or other herbal defects, pay attention to use and stone colour close to the glue to restore.
Grinding is the complete countertop surface grinding process, the same grinding gloss necessities of greater than 90 °, at the same time the surface right into a replicate luster, no bump, no wave pattern, the intersection of straightness to maintain a straight line in a immediately line, the counter tops and washbasin mouth of the gloss ought to be similar to the day floor consistency. Usually with a handheld mill to grind, if exact outcomes, to be had large mill grinding.
For a aggregate of more than one parts of the countertop ought to be prepare to repair and sanding, so as now not to watch for the time when the take a look at spelling issues.
Trial assembly inspection
The countertop could be inspected piece with the aid of piece, and the substandard products are located to be replaced or reworked in a timely manner. At the identical time for the combination of countertops is not a single product further to the requirements of the brink of the smoothness, experience and flatness of the plate, and many others., however also must try to put together a aggregate, be aware of the combination of countertops among the team spirit of the shade, the interface of the collocation, in addition to the combination of the left and right order have to be in accordance with the drawings accurately.
For the bad impact of the collocation to rework, for the shade is not uniform to be replaced.
Usually, if the hole of the washstand is best or much less than 7 or 8cm from the brink, it wishes to be strengthened with metal bars. Even if extra than this distance, if the client has a request need to be bolstered on the lower back of the metal. After the inspection, if the customer has the requirement to do the safety (water-proof remedy, and so on.), then we will do the safety.
Packing
Packaging according to patron requirements or stone first-rate of the product packaging, blunt floor and blunt surface of the alternative, within the smooth surface among the clip anti-scratch gentle movie sheet. As for a number of the concern of scratching the stone, like the overall colour of darker stone (together with Shanxi black), in an effort to save you scratches have an effect on the visible impact might be wrapped in movie processing. Countertop panel should be positioned vertically, so that the stone longitudinal like pressure, do no longer placed horizontally. The first-rate packing tape package all the counter tops bundled into a whole, do not loose.
Finally, the paintings is finished, the countertop is so produced and packaged, can be shipped.
Natural stone antique floor and its processing manner creation
In the beyond years, because of the exchange of stone design and ornament trend, the antique processing of natural stone is an increasing number of extensively utilized in all varieties of architectural ornament and ornament, very lots cherished and preferred by way of architects and customers. In truth, the vintage surface of herbal stone is not a new processing technique advanced only in latest years, as early as in the 1990s there has been. Used in our country is likewise very early, which includes the development of Beijing in 2001, “National Grand Theater” on the part of the usage of this thru the vintage treatment of stone.
What is antique stone?
The so-called “vintage stone”, is the herbal granite or marble by way of special treatment, so that the surface of the stone seems similar to the weathering of the herbal wave or cracks, at the same time as the stone after a long duration of use and the herbal put on impact (similar to the impact of matte or satin). Commonly written, is the natural stone processing just like the use of hundreds of years after the vintage effect.
Advantages of stone antiquing
Stone vintage processing will have uneven satin satin effect, displaying the herbal crystal luster of the stone, play a unique ornamental impact; on the equal time additionally improve the stone stain resistance and water-proof performance, and can play a non-slip role. Stone vintage processing can also be averted due to the reflect reflection of the constructing mild and light pollutants. At the identical time antique stone put on and tear is simple to restore. At the equal time the color difference is smaller than polished processing, but also higher reflect the fee of natural environmental safety idea.
Natural stone antique processing of the main equipment
Stone vintage processing of the principle equipment is stone grinding brush ((Abrasive Brushe), it mainly has 3 kinds: nylon brush, wire brush and combined brush.
Nylon brush is product of tremendous silicon carbide and special nylon cloth synthesized abrasive cord, firmly fixed in a broom base made, specifically used for marble vintage grinding brush. Steel wire brushes, on the other hand, are fabricated from stainless-steel or moderate metal wire and are especially used for brushing difficult stones such as granite. Mixed brush, that is, by the unique nylon and chrome steel cord product of abrasive brush.
Stone abrasive brushes are categorized in line with specifications, which includes Frankfurt type (horseshoe), round, Fekete kind (Bra kind), and so forth.; in line with the mesh number category: twine brush, 36#, 46#, 60#, eighty#, a hundred and twenty#, one hundred eighty#, 240#, 320#, 500#, and so on.. Among them, Frankfurt kind is used in stone industrialized manufacturing of hand held grinding system, grinding and sprucing production line, floor protection machine, etc.; spherical for small guide sharpening device, ground preservation device, and so forth.; Fiktor type is used in automated non-stop grinding device.
Processing flow of antique surface of natural stone
Because the material and structure of granite and marble are exceptional, every has its personal traits, so the processing of granite vintage stone and marble vintage stone is not the identical.
Granite antique surface processing
Due to the difficult texture of granite, the primary way to use fireplace or high-pressure water dashing of granite plates processed into a rough surface of the fireplace plate or rough panel (also can be processed into the lychee sandblasted floor and so forth, however the impact is not very good), pay attention to the processing into a rough hard bushy floor must be rougher than the normal burnt plate, so you can keep away from using the subsequent step inside the stone grinding brush while the stone plate is just too easy to make the layout layout to lose the experience of 3-dimensionality.
Then use the stone grinding brush for brushing, observe that it is first-class to use a twine brush first; to perform a hard brush, push aside the unfastened granite plate surface and shaping, so now not most effective high performance, however also on the wear and tear and tear of the system is small, can expand the service existence of the grinding brush.
After that, in line with the consumer's precise necessities, using coarse mesh range to great mesh variety of grinding brush sequence grinding and sharpening, till the plate surface to obtain the desired impact and luster. If the purchaser calls for to attain a easy matte effect best need to pick out the metal brush, 36 # (or 46 #), 60 # (or 80 #), one hundred twenty # (or a hundred and eighty #) 4 methods could be desirable; if you need to obtain the effect of satin, you need to feature 240 #, 320 #, 500 # three processes, of path, if all of the procedures will do a higher end result. As for a few no gloss necessities of a few outdoor plate may be used at once with a twine brush grinding brush is right.
Marble vintage surface processing
Because of the material of different marble is very distinctive, so have to be based totally on the sorts of marble characteristics of the differences within the choice of processing methods.
Containing more calcium and magnesium carbonate or cracks and holes within the marble may be corroded with hydrochloric acid immersion, immersion time of approximately 10-20 mins (in line with the unique stone varieties to determine); after the usage of a metallic brush to assault the cracks and holes in the residue to boom the three-dimensional sense of the floor of the stone, the ultimate is to apply the wide variety of coarse mesh to the variety of quality mesh of the order of the abrasive brush grinding and sprucing until the plate to acquire the purchaser's requirements of the luster.
If the table calcite greater marble may be without delay processed by way of steel brush, the same may be first brushed with metallic twine brush out of the uneven three-dimensional floor effect, observed by means of a number of coarse mesh to excellent mesh grinding brush collection grinding and sharpening, usually the usage of one hundred eighty #, 240 #, 320 #, 500 # of grinding brush to method on it, if it's miles the texture of the marble is tremendously hard to appropriately boom the first few processes.
Reinforcement of natural stone slabs and its method
Nowadays, an vital development trend of herbal stone slabs is thinning, and stone practitioners in various international locations have taken the thinning of slabs as one of the principal directions of latest product development. This makes the current stone skinny plate thickness may be reduced over and over, heavy earlier 15mm to 12mm, and then 10mm, till now 8mm, 6mm, that is most effective via the body plate, if the stone composite plate has reached 3mm.
However, with the stone thickness is getting thinner and thinner, an unavoidable hassle has arisen, is because of the shortage of popular bending power, ensuing in an boom in the breakage price of the stone thin plate, like the ones of the softer material marble, limestone and sandstone, and many others. Is particularly clean to start breakage. So how can we lessen the breakage charge of stone sheet? There is best one manner to go, is to increase the bending and flexural electricity of the stone, that is to mention, the stone line ought to be bolstered.
So how to beef up the stone?
Usually for the stone thru the frame plate skinny plate we usually have approaches to enhance, one is the again of the stone plate “back community” reinforcement; one is the surface of the stone plate to penetrate the reinforcement.
Plate “back community” reinforcement
Plate “again community” reinforcement is thru the epoxy resin may be very excessive strength fiber safety community bonded to the back of the plate and drying, in order that the power of the plate to be bolstered. Usually the stone plate “returned internet” reinforcement is our first preference for plate reinforcement, due to the fact it's miles the most comparatively cheap and affordable way of reinforcement.
Usually the manufacturing unit is the choice of mesh specs for the 5X5MM, unit weight of 900g/M2 fiber mesh, the whole roll of fiber protection network width from 1.2-1.8M there are numerous exclusive specifications, in step with the unique size of the plate to choose. As for the epoxy resin requirements do no longer need any unique requirements, as long as the everyday epoxy resin may be, low, medium and excessive viscosity series of epoxy resin can be used for the reinforcement of the plate. Reinforcement of the plate is the most used low viscosity collection of epoxy resin, commonly at 25 ℃, the solidification time is ready 30-50 mins, in case you growth the percentage of curing agent, a few low-viscosity epoxy resin may be 30-40 mins solidification, a few low-viscosity epoxy resin can be shortened even to eight-12 minutes. However, it generally takes 24 hours for epoxy resin to attain full curing at room temperature, and the time of complete curing may be appreciably shortened if the heating approach of drying oven is adopted.
Solidification time is an crucial process parameter for backsheet reinforcement, which relies upon at the wide variety of sheets to be backsheeted, the output, the operation mode of the backsheet technique, and whether or not a drying oven is used or not, or the drying ability of the oven and different factors. If the wide variety of panels to be reinforced inside the manufacturing line is huge and the output requirement is high, the mechanized again-screening reinforcement method can be adopted, and the herbal and complete curing method at room temperature or the flat-plate curing and heating drying oven may be selected. If the output requirement could be very excessive, even vertical drying oven may be chosen, which should be used with low viscosity epoxy resin proportion with shorter solidification time. And a few manufacturing lines with low output can undertake artificial returned-netting operation, natural and complete curing approach at room temperature, and pick low viscosity epoxy resin percentage with especially gradual solidification time to lessen the investment of manufacturing line equipment.
Surface penetration reinforcement of the plate
We realize that the stone is a lot of mineral polymerization, its microstructure has lots of voids, there might be many micro cracks, and even cracks, and a few cracks can be deep into the depths of the plate to head, specifically for marble. And a few stone in the “returned community” after reinforcement of its power nevertheless cannot meet the necessities of grinding and sprucing method or qualified finished plate corresponding to the technical necessities. Then we can be on the surface of those plates to penetrate the reinforcement, that is, so that the permeability of the epoxy resin glue through the stone's very own voids and cracks penetrate into the inner stone to go, after drying (drying) processing, in order that the stone will become a cemented complete, thus reinforcing the stone, to improve the energy of the stone plate.
Pay interest to the floor penetration reinforcement of the plate, use the low viscosity epoxy resin with accurate permeability to carry out the surface penetration reinforcement treatment. Because if the solidification time is too brief, the epoxy resin cannot absolutely penetrate into the interior of the plate, so the impact of reinforcement will be significantly decreased. Generally, the low viscosity epoxy resin used for floor penetration reinforcement of the plate has a long solidification time, commonly extra than 50 minutes. However, there are some properly permeability of low viscosity epoxy resin, its solidification time is only 15-half-hour, but can most effective be used in the cracks and voids on the thick stone plate. If you need to gain right reinforcing effect, it's far nice to pick a long solidification time of excessive permeability epoxy resin.
Usually the solidification temperature of epoxy resin for surface penetration reinforcement is also approximately 25 ℃, the lowest curing temperature is 10-15 ℃, the whole curing time at room temperature calls for 24 hours. For the pursuit of high production stone production line, you may use flat plate horizontal drying oven or vertical vertical drying oven and different drying system, in order that the surface penetration of the plate after reinforcement of excessive-temperature curing treatment, so as to accelerate the complete curing of epoxy resin. If it's miles a smaller manufacturing of stone production line, may be used at room temperature natural curing approach, however as a minimum 24 hours to make the plate to get absolutely solidified, entire the reinforcement of the plate.
There are many forms of stone, unique shades, or even the identical type of sun shades of its differences, so the natural stone plate floor penetration reinforcement treatment have to do not forget the epoxy resin and plate coloration of the identical diploma and with the diploma. If you ignore this factor will trade the original coloration of natural stone, and lead to the whole batch of plate scrap. However, in recent times for plate reinforcement of epoxy resin sorts and colours also are very diverse, generally can find the relevant shade. Therefore, the most crucial aspect is that there may be no hint of the use of epoxy resin after the reinforcement of the surface penetration of the plate the usage of epoxy resin. At the identical time, we additionally need to recollect the use of the environment of the plate, in spite of everything, unique epoxy resins have their temperature and climate conditions of use, and within the choice of epoxy resins should first keep in mind the use of the environment of the plate.
Leave a Comment